Steel Building Planning Guide – What Needs to be Done?
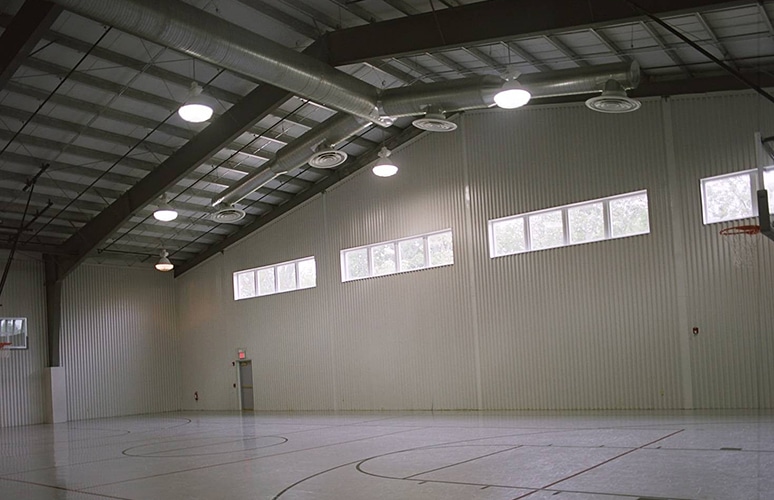
As with any building project, purchasing and erecting prefabricated metal buildings requires meticulous planning. As a rule, a better-planned project has a better chance of going more smoothly. This article will give you some key information to help you plan for and seamlessly execute your next metal building project. We will expand on the planning stage by first focusing on the two major factors you need to consider:
- Practical considerations
- Legal considerations
Practical Considerations
A good starting point is to think about how you intend to use the building. For instance, if you are building a storage warehouse, you will need to factor in high roll-up doors that can accommodate your forklifts and tall shelving. If you’re constructing an agricultural building for housing livestock, it will require adequate ventilation. Alternatively, while metal buildings require foundations, typically flat concrete slabs, your use may require you to use another type of foundation. On top of that, you will need to ensure the following is available onsite:
- Firm and level ground
- Natural drainage
- Ease of access
- Access to utilities
- Room for possible future expansion
Legal Considerations
Every province and state will have different building codes that you need to comply with when planning for and constructing your project. These codes can include things like wind and snow loads. Since these codes are constantly changing, you need to check with your county or city planning department to make sure you understand all the current guidelines. TORO Steel Buildings will also ensure that your building is engineered to meet all published wind, snow and seismic loads for your location.
Other legal requirements you need to consider include:
- Draining requirements
- Zoning laws
- Energy codes
Some cities or counties have stricter energy codes. This can include requiring you to use more insulation in order to reduce your building’s carbon footprint and complying with green building standards. This upfront investment of heavier insulation will make your building more energy-efficient, thereby reducing heating and cooling costs. In most cases, you will recoup the investment within the first year in cost savings.
With that said, it is not all black and white. Some aspects of your design will require both legal and practical considerations. For instance, if you are setting up a retail store, you will need and are legally required to provide handicapped access and appropriate parking.
Physical Building Considerations
Building Orientation
Depending on the intended use of your building, sun exposure and wind direction might be important to you. For instance, when do you prefer to have the sun shining through the windows, morning, afternoon or early evening? Do you want to highlight a particular view? These are some of the things you will need to think about when deciding on the orientation of your building.
Building Size and Dimensions
It is often better to plan on purchasing a building that is larger than what you think you need, as you will almost certainly grow into the extra space faster than you think.
Some common standard steel building sizes include 30×40, 50×100, 60×40, and 60×120. When deciding on the final size for your structure, it is wise to go one size larger than what you initially think you need
Building Height
The standard heights of single and multi-story buildings are typically governed by local codes. However, as a rule, the building eave height must be taller than the highest framed opening by at least two feet. For arch buildings specifically, the clearance over the framed opening must be a minimum of one foot, but it could be more depending on the door size and type.
Roof Pitch
You can use the desired amount of clear space in the middle of the room to design the shape of the roof. Roof pitch ratio is used to express the slope of the roof. This is the number of inches of rise in 12 inches of horizontal length, is displayed as a colon between the two numbers. For instance, a roof with a 2:12 pitch means that for every 12 inches of length, the roof slopes up 2 inches. This can also be indicated in feet when discussing larger structures.
Framed Openings
This is a term used to describe any opening in the building that is larger than a standard doorframe, whether it contains a door or not. In general, these are large openings through which equipment, vehicles and loading items pass through like a garage doorway. Retail stores, schools and manufacturing facilities often require a loading bay area, closed off by a massive door, where trucks can back up to pick up or deliver items.
Long-Term Benefits of Prefabricated and Pre-Engineered Steel Buildings
Huge Energy Savings with High-Grade Insulation
Metal buildings used for storage, aviation, garages or warehouses may not need heating and air-conditioning in mild climates. However, commercial, industrial, residential and institutional buildings where people are employed or spend time require climate control systems. In these circumstances, prefabricated metal buildings work especially well. Their energy-efficient insulation options typically reduce heating and cooling costs by as much as 50%. For extremely hot climates, using cool coated roofing panels also reduces your energy costs by another 7 to 15 percent.
Low Maintenance on High-Quality Steel Buildings
Unlike wood, steel is mold, rust and pest-proof. This means that you will not have to spend money on pest control, repairing termite damage, repainting, or removing mold. Additionally, steel framing does not warp, split, rot, or twist like wood. A steel building continues to give you the same reliable service for decades, with only minimal maintenance.
Fewer Foundation Problems with Metal Buildings over Time
Unlike wood-framed buildings, steel buildings require fewer framing pieces, which lessens the strain on the foundation. This translates into less settling and therefore reduces the chance of expensive foundation problems over time.
Metal Buildings Retain their Value Longer
The sturdy steel wall panels and roof panels on structures from Toro Steel guarantee that they will stay straight and true for years. The framing is designed to meet and exceed the expected loads for the lifetime of the building, allowing it to retain its original beauty and value exceptionally well throughout the years.
Contact Toro Steel to Begin Planning Your Metal Building
If you are interested in prefabricated metal buildings and are looking to get started on your steel building project, now is the best time to talk with our experts. We can guide you from start to finish, helping you save both money and time in the process. Contact Toro Steel Buildings today to learn more about how we can help you or to inquire about our prefabricated steel buildings for sale.
Related Post
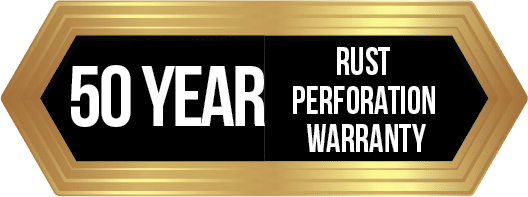